Ccbts Cu Ccshorts Cu Yaoua Ccshorts Cu Ccyoutube Cu

Shorts вђ Cubic Online Store Cu carbon nanotube (cnt) composites that merge copper with cnts are touted to fulfil the growing need for cu substitutes [8 – 17]. cnts are expected to play two roles in cu cnt. (i) made of carbon, cnts act as weight reducers, rendering the composites lighter. (ii) cnts could transmit their own exceptional nanoscale multifunctional properties. 2.1 samples preparation. the materials and details of the fabrication of cnts cu foams and cnts cu f ®cu composites were described in our previous work [19, 23].figure 1 shows the schematic illustration for preparing the composites through powder metallurgy, during which the densification is mainly achieved by sps, which provides extremely fast heating and cooling rates, a short holding time.
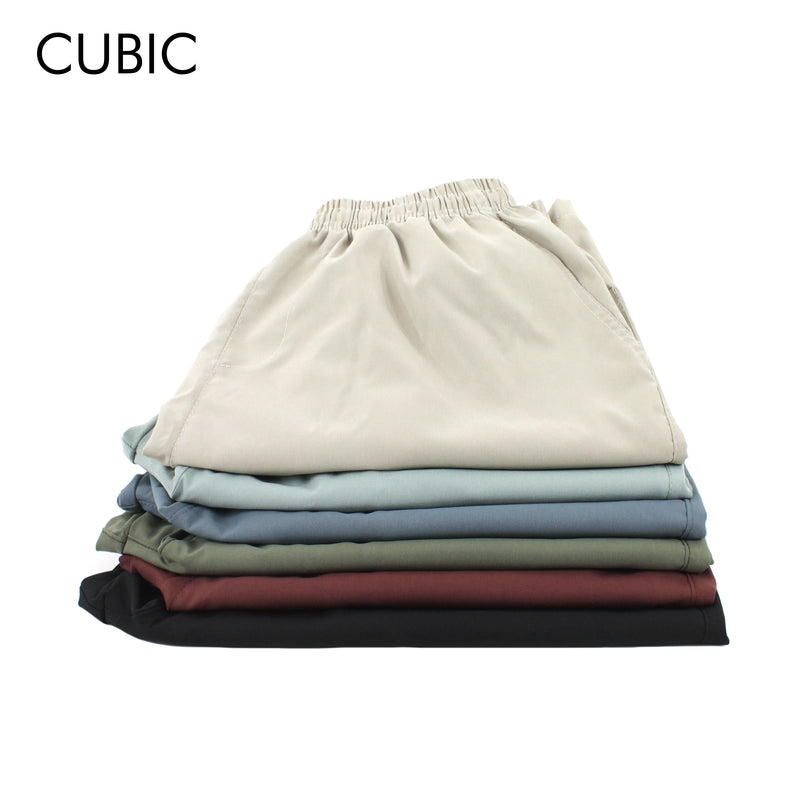
Shorts вђ Cubic Online Store The power losses associated with the electrical resistance of copper (cu) have generated considerable interest in the development of advanced conductors that incorporate carbon nanotubes (cnts) into the cu matrix—ultraconductive cu (ucc) composites—to increase energy efficiency in various industrial and residential applications, ranging from electric power transmission and rotating. The ni plating was the most dense, continuous, and complete. the strengthening effect of ni@cnt with respect to the cu matrix is the greatest, but its elongation and conductivity decreased greatly. the cu@cnts cu composite achieved the balance of mechanical properties, ductility, and conductivity thermal conductivity. Carbon nanotubes (cnts) are considered ideal nanoscale reinforcement for the development of high performance metal matrix composites due to their unique structure and excellent mechanical properties. however, cnts are easy to agglomerate and have poor wettability with the aluminum matrix, resulting in unsatisfactory effects when added to the aluminum melt. in this study, cu coated carbon. The wear width was reduced from 965 μm to 836 μm, so the wear resistance was significantly improved. the coefficient of friction (cof) and wear of the two materials are summarized in table 2. the 3d interconnected cnts cu composites exhibited better anti friction properties (cof ≈ 0.22) compared the cof for cu is 0.55.
Comments are closed.