Control Motor Forward Reverse Plc Ladder Program

Plc Program To Control Motor In Forward And Reverse Direction Sa Plc example for motor. the workpiece starts moving on the left side and moves to the right when the start button is pressed. when it reaches the rightmost limit, the drive motor reverses and brings the workpiece back to the leftmost position again and the process repeats. the forward and reverse pushbuttons provides a means of starting the. The ladder logic program for the automatic reverse forward motor control using the s7 1200 plc consists of two parts: the main program and the subroutines. the main program is responsible for the overall control of the motor, while the subroutines perform specific tasks, such as controlling the direction of rotation of the motor. related posts:.
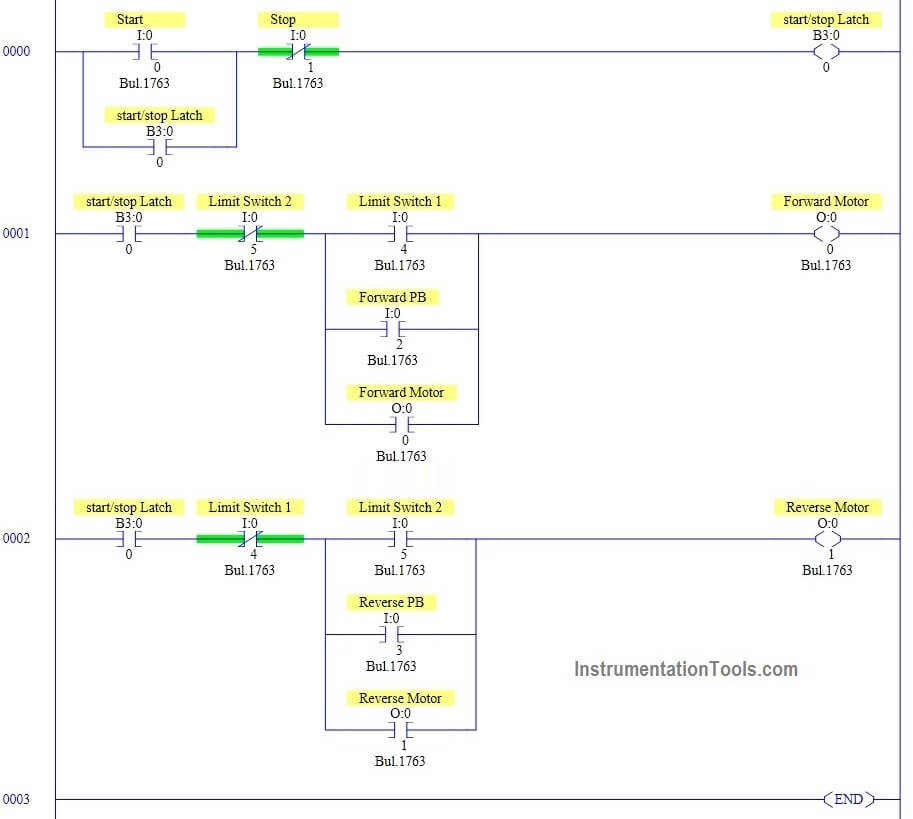
Plc Programming Example For Motor Forward And Reverse Control Plc program to control motor in forward and reverse. This video tutorial will teach plc programming for automatic motor forward and reverse control using ladder logic.## learn plc programming using examples ##1. The forward and reverse motor commands will operate normally if no overload condition exists because the overload contacts will provide continuity. however, if an overload occurs, the contacts in the plc program will open and the motor circuit will turn off. the overload indicator pilot lights (ol fault fwd and ol fault rev) use latch unlatch. Ladder logic description. in this application, we will use siemens s7 1200 plc and tia portal software for programming. we can also design this logic with relay circuit. this circuit is also known as forward reverse control for 3 phase induction motor. we will write logic for forward condition in network 1.

Plc Programming For Automatic Forward Reverse Motor Control Yout The forward and reverse motor commands will operate normally if no overload condition exists because the overload contacts will provide continuity. however, if an overload occurs, the contacts in the plc program will open and the motor circuit will turn off. the overload indicator pilot lights (ol fault fwd and ol fault rev) use latch unlatch. Ladder logic description. in this application, we will use siemens s7 1200 plc and tia portal software for programming. we can also design this logic with relay circuit. this circuit is also known as forward reverse control for 3 phase induction motor. we will write logic for forward condition in network 1. In this section the user can toggle the forward button on and off (since the forward switch behaves as a push button). now forward timer starts, after 5 sec the forward motor goes to on stage. 18. before start the reverse motor, the forward motor should be stopped. now the reverse button can be toggled on and off. Ladder logic program for motor control is explained below. there are two motor m1 and m2 one allows forward rotation and the other one allows reverse rotation. to keep the motor running even after the operator removed its control switch (s), we could change the circuit in several different ways: we could replace the pushbutton switches with toggle switches, or we could add more logic of relay.
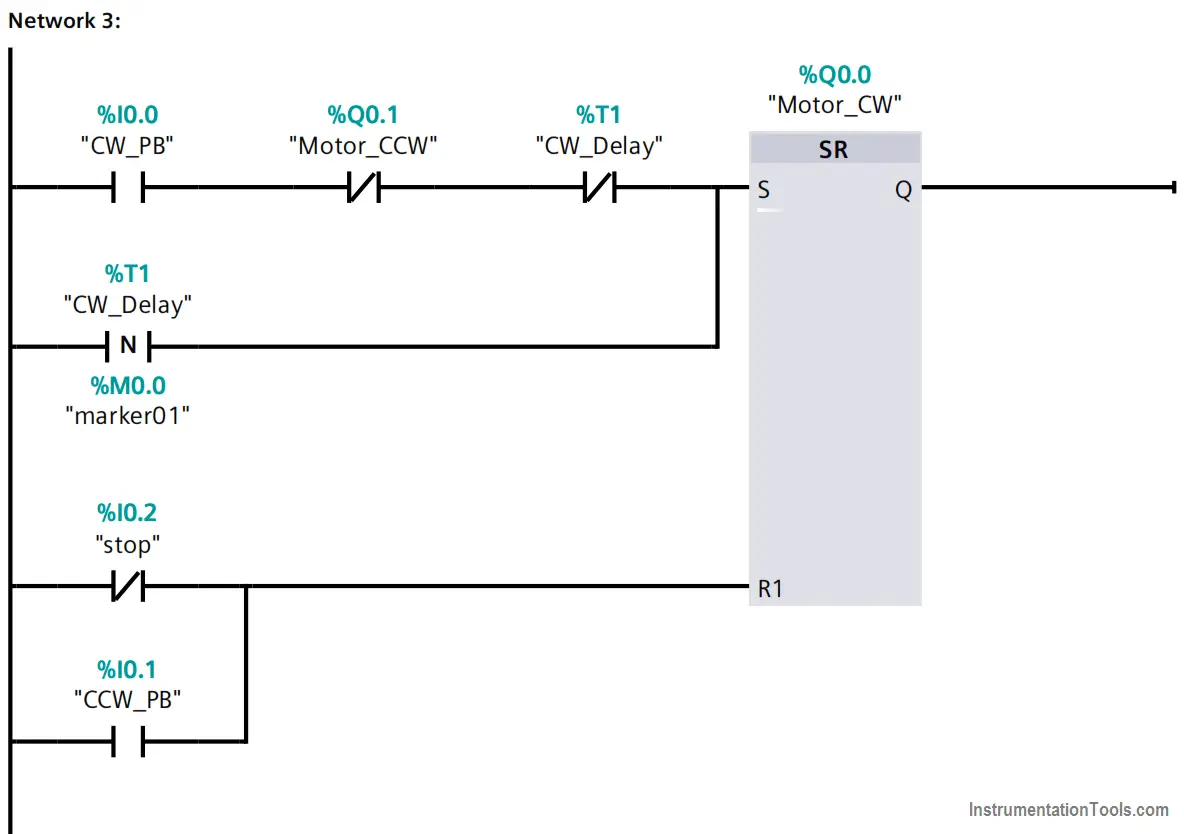
3 Phase Forward Reverse Motor Control Circuit Diagram With Timer In this section the user can toggle the forward button on and off (since the forward switch behaves as a push button). now forward timer starts, after 5 sec the forward motor goes to on stage. 18. before start the reverse motor, the forward motor should be stopped. now the reverse button can be toggled on and off. Ladder logic program for motor control is explained below. there are two motor m1 and m2 one allows forward rotation and the other one allows reverse rotation. to keep the motor running even after the operator removed its control switch (s), we could change the circuit in several different ways: we could replace the pushbutton switches with toggle switches, or we could add more logic of relay.
Comments are closed.